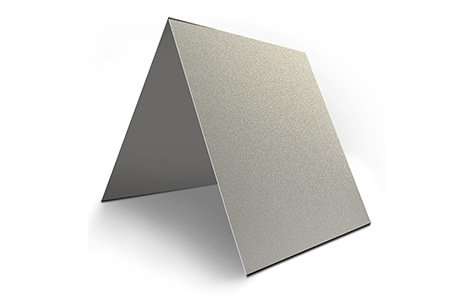
Anodized Aluminum Plate
Chalco-produced anodized aluminum plates have advantages such as consistent color, high-quality sealing, and corrosion resistance for the entire batch of products.
Depending on the intended use of the product, Chalco can also use various anodizing techniques to produce aluminum plates in different colors. Transparent, bronze, gold, and black are the most favored anodized colors by customers.
Chalco anodized aluminum plate production standards
- ASTM B632, B209
- AMS-QQ-A-250/2
- Mil-A-8625
- AAMA 611-11
- ASTM B-117: Plate Bar Spray Test Method (Salt Spray Test)
- ASTM B-680: Test Method for Seal Quality of Anodic Coatings
- ASTM B-523: Test Method for 60° Specular Gloss of Anodized Aluminum Surfaces
- ASTM B-137: Test Method for Measurement of Coating Mass Per Unit Area on Anodically Coated Aluminum
Chalco anodized aluminum plate display
Multi-tone anodized aluminum plate
Anodized aluminum plates offer significant flexibility in design with their diverse range of color options, catering to various styles and preferences.
Whether you are seeking the modern and stylish aesthetics of black, the vibrant appeal of transparent colors, or other warm-toned hues, you can find your preferred choice at Chalco.
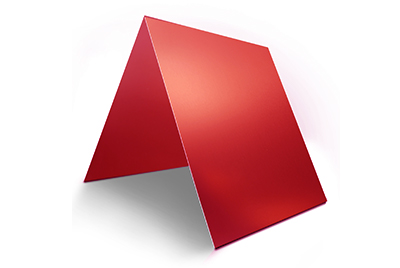
Red anodized aluminum plate
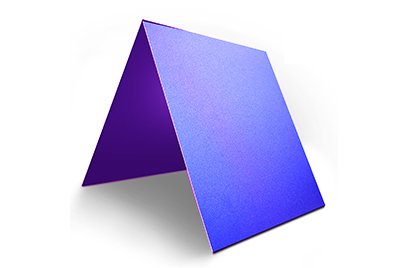
Clear anodized plate
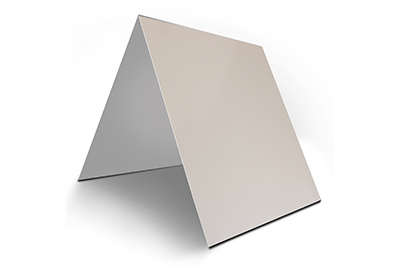
White anodized aluminum plate
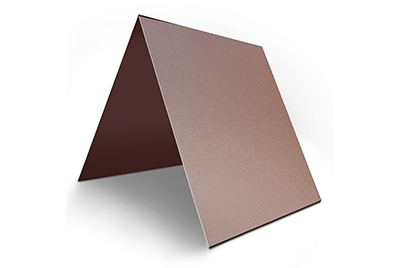
Bronze anodized aluminum plate
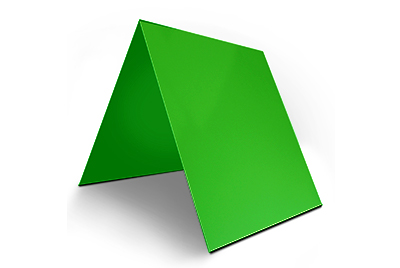
Green anodized aluminum plate
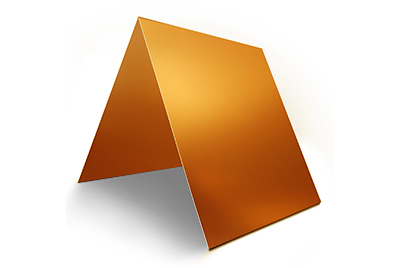
Orange anodized aluminum plate
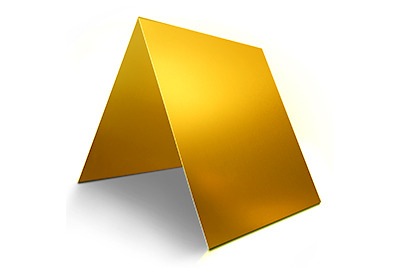
Yellow anodized aluminum plate
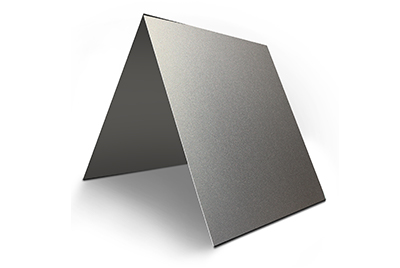
Silver anodised aluminium plate
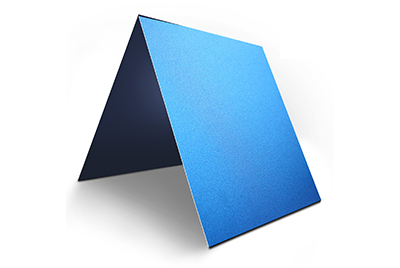
Blue anodize aluminum plate
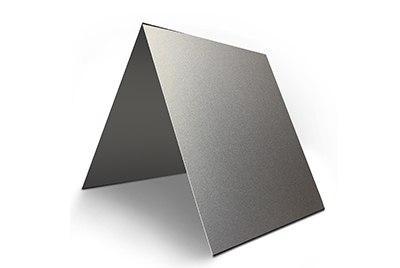
Gray anodized aluminum plate
Anodized aluminum plate alloy series overview
Chalco anodized aluminum sheets are made from Series 1, Series 3, Series 5, and Series 6 alloys.
We offer common size options including thicknesses of 0.025'', 0.032'', 0.04'', 0.05'', 0.063'', 0.08 '', 0.125'' 4' x 6', 4' x 8', 4' x 10' size aluminum panels.
-
1050 anodized aluminum plate
Thickness: 0.2-500 mm
Application: Nameplates, decorations, containers
-
1060 1070 anodized aluminum plate
Thickness: 0.2-350 mm
Application: Chemical containers, battery casings
-
1100 anodized aluminum plate
Thickness: 0.40-152.4 mm
Application: Printing plates, kitchen utensils
-
3003 anodized aluminum plate
Thickness: 0.2-250 mm
Application: Kitchenware, curtain wall panels
-
5005 anodized aluminum plate
Thickness: 0.2-250 mm
Application: Furniture, signs, auto parts
-
5052 anodized aluminum plate
Thickness: 0.2-250 mm
Application: Vehicle and ship sheet metal parts, fuel tanks
-
5083 anodized aluminum plate
Thickness: 0.2-400 mm
Application: Pressure vessels, pattern plates, armor plates
-
5086 anodized aluminum plate
Thickness: 1.60-25.4 mm
Application: Signs, corrugated boards, armor plates
-
5754 anodized aluminum plate
Thickness: 3.0-50 mm
Application: Ship boards, wall panels, kitchenware, aerospace
-
6061 anodized aluminum plate
Thickness: 0.2-250 mm
Application: Vehicles and ships, mcurtain wall panels, hardware
-
6063 anodized aluminum plate
Thickness: 0.483-199.5 mm
Application: Building railings, windows, cylinders
-
6082 anodized aluminum plate
Thickness: 0.5-300 mm
Application: Bridges, decorative panels, aircraft skins
Note: For 2xxx, 4xxx, and 7xxx series aluminum plates, due to reasons such as process, performance, and color, anodization is generally not required for routine applications.
If you do require anodization for these products, please consult with us promptly. Chalco is a professional anodizing manufacturer.
Anodized aluminum plate application classification
Chalco anodized aluminum plates feature a multifunctional design that can be easily shaped to meet your specific application requirements through processes such as cutting, shearing, bending, punching, and more.
-
Anodizing aluminum plate for electronic products
Film thickness: 2.5-30μm
Color: Transparent, champagne, gold, silver, gray, bronze, etc.
-
Anodizing aluminum panels for home appliances and furniture
Film thickness: 2.5-30μm
Color: Silver gray, black, white, silver, gold, etc.
-
Anodizing cookware, lampshade, road sign strips
Film thickness: 2.5-30μm
Color: Silver white, black, gold, blue, red, yellow, etc.
-
Anodizing automobile aluminum plate
Film thickness: 2.5-30μm
Color: Silver white, gray, black, transparent color
-
Anodizing architectural decorative plate
Film thickness: 2.5-30μm
Color: White, gray, black, silver, light brown, turquoise, etc.
-
Anodizing aviation aluminum plate
Film thickness: 2.5-30μm
Color: White, silver, gray, black
-
Anodizing craft aluminum plate
Film thickness: 2.5-30μm
Color: White, silver, dark copper, gray, yellow, gold, black, etc.
-
Anodizing ship aluminum plate
Film thickness: 2.5-30μm
Color: Silver, white, gray, black, gold, blue
Special anodized aluminum plate
We not only offer traditional anodized aluminum sheets but also provide various special types, including hard anodized aluminum sheets, micro-arc oxidized aluminum sheets, and anodized functional film aluminum sheets, to offer you a wider range of choices for your specific needs.
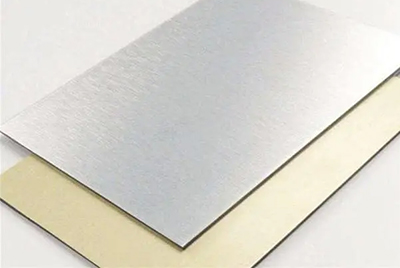
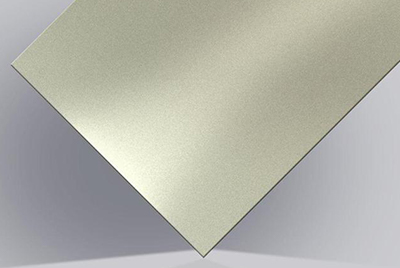
Micro arc oxidation
Spark Anodizing is a type of micro-arc oxidation film generated under high temperature and high-pressure conditions.
Contact us nowAnodized Functional Film Sheet
Types: Electromagnetic Film Aluminum Sheet, Separation Film Aluminum Sheet, Photoelectric Film Aluminum Sheet...
Contact us now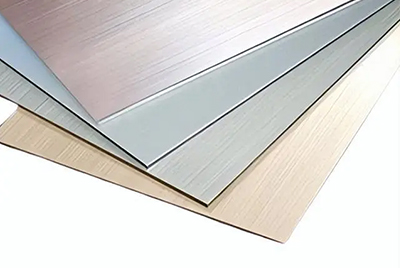
Advantages of anodized aluminum plate
- Anodized aluminum sheets exhibit high corrosion resistance and can be applied in harsh environments.
- After treatment, anodized aluminum sheets increase in hardness, enhancing surface durability.
- Anodized aluminum sheets can undergo staining and coloring, adding aesthetic and decorative qualities.
- The anodized oxide film improves adhesion on the surface of aluminum sheets, ensuring a more robust coating.
- Anodized aluminum sheets possess high electrical resistance, with insulation breakdown voltage reaching up to 200V/μm.
- The high transparency of the anodized oxide film maintains the original metallic luster of anodized aluminum sheets.
- Leveraging the porosity of the anodized oxide film allows for the deposition of functional particles, enabling various functional applications.
Chalco anodized aluminum plate quality assurance
- Chalco's anodized aluminum sheets utilize advanced production processes to ensure uniform and consistent color without any color deviations.
- Chalco rigorously controls the thickness of the oxide film.
- Chalco's anodized aluminum sheets exhibit high-quality sealing, free from imprints and fingerprints.
- Chalco's anodized aluminum sheets demonstrate outstanding corrosion resistance, weather resistance, and wear resistance.
- Chalco's anodized aluminum sheets feature high hardness, coupled with strong adhesion.
Chalco anodized aluminum plate frequently asked questions
Anodized aluminum plate process
Cost To Anodize Aluminum
The size and color are the primary factors affecting the cost of anodized aluminum sheets. Larger sizes result in larger surface areas, requiring more stringent solutions, equipment, and processing conditions. Additionally, processing certain specific colors can also increase construction costs.
As a result, the price of anodized aluminum sheets is influenced by these factors. If you require specific cost information, feel free to consult with us to obtain accurate pricing for anodized aluminum sheets.
Chalco anodising solution selection
Sulfuric Acid Anodizing Sulfuric acid anodizing is a commonly used, cost-effective method. The resulting oxide film has high transparency, excellent corrosion resistance, good wear resistance, and is easily colorable.
Chromic Acid Anodizing Chromic acid anodizing produces a relatively thin oxide film with a soft and elastic texture. The color after anodizing ranges from light gray to dark gray. This method is suitable for surface treatment of castings, riveted parts, and machined components.
Oxalic Acid Anodizing Oxalic acid anodizing yields an oxide film with low porosity, offering good corrosion resistance, wear resistance, and electrical insulation. However, it has higher production costs, poorer electrolytic stability, and is prone to color variations. Typically, it is only employed for special applications such as insulation protection for motors and surface decoration of daily-use items.
Phosphoric Acid Anodizing Phosphoric acid anodizing is mainly used for electroplating pretreatment of aluminum sheets, surface treatment of printed metal sheets, and pretreatment for adhesive bonding of aluminum sheets.
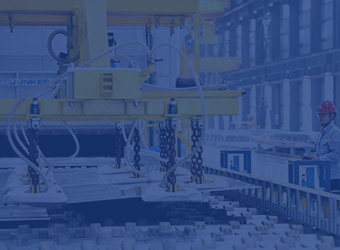